SUCCESS STORY
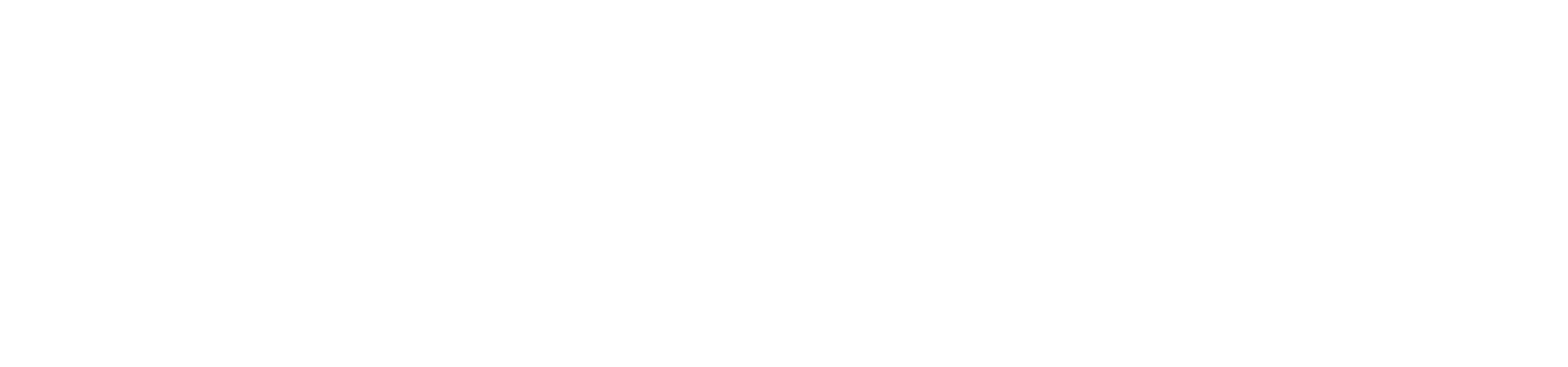
Zero equipment breakdowns in key areas
Transforming Performance with World Class Manufacturing (WCM)
- How Armacell enhanced reliability, reduced waste, and improved operational efficiency across 23 global sites
Outcomes
Improved operational performance
- TPM implementation reduced equipment breakdowns to zero in key areas
- Majority of plants achieved Bronze-Level WCM certification, with several advancing to Silver-Level
- Standardised processes enhanced production efficiency across sites
- Problem-solving shifted from quarterly reviews to real-time interventions
- Teams adopted structured methodologies for addressing recurring issues
Stronger leadership and workforce engagement
- Daily control and structured leadership involvement accelerated the pace of improvements
- Shopfloor teams gained confidence and expertise in continuous improvement methods
BACKGROUND
Armacell is a leading global manufacturer of advanced insulation and engineered foam products, with 23 plants in 16 countries across four continents.
To strengthen its operational capabilities, Armacell had launched the World Class Armacell Mindset (WAM) Programme, built on World Class Manufacturing (WCM) principles, including Total Productive Maintenance (TPM) and Lean methodologies.
the challenge
Despite Armacell’s strong market position, the company faced several key challenges in its manufacturing operations:
- Inconsistent plant reliability across sites, leading to unplanned downtime and inefficiencies
- High material loss due to process instability
- Lack of standardisation in maintenance practices and problem-solving approaches
- Limited workforce engagement in continuous improvement initiatives
These challenges not only impacted operational efficiency but also added unnecessary costs and complexity to the company’s global supply chain.
our solution
To address these challenges, Armacell partnered with Henkan to implement our WAM Programme. The initiative focused on three core strategies:
-
Implemented Autonomous Maintenance (AM) and Professional Maintenance (PM) to restore key equipment controls and reduce downtime. A daily control system enabled real-time resolution.
-
Applied Lean and Focused Improvement (FI) initiatives to reduce material loss and optimise workforce. A structured audit system measured WCM progress across plants.
-
Delivered WCM ‘Practitioner Courses’ and shifted problem-solving to daily, weekly and monthly cycles. Leadership engagement increased through support systems such as Morning on the Shopfloor.
“Henkan’s expertise accelerated our WCM journey, ensuring consistency and impact.”
HNK104